
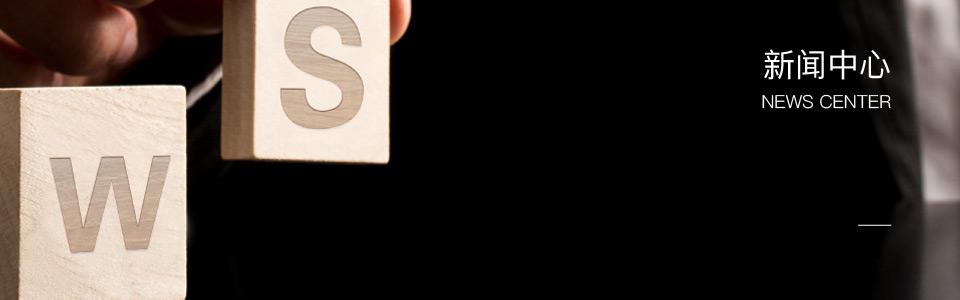
行业资讯
INDUSTRY INFORMATION
2021-12-08
订单总量超12GW!西门子歌美飒2024年起交付14-15MW风机
西门子歌美飒近日发布了叶轮直径长达236米的最新型SG 14-236 DD海上风机。凭借该机型,西门子歌美飒已成为英国3.6 GW Norfolk项目的首选风机供应商,该项目是全球最大的海上风电场之一。西门子歌美飒海上风电全球产品组合管理负责人Martin Gerhardt表示,将从2024年开始交付14-15MW的海上风机,这是西门子歌美飒基于成熟的直驱型海上风力发电技术推出的第六代海上风机。截止目前,第六代风机的在手订单总量已超过12GW。为此,公司将加速产能建设,并提升供应链效率,以应对即将来临的大规模海上风机安装。“我们是在对SG 14-222 DD海上风机的零部件进行测试的过程中,发现并验证将叶片从108米增至115米的可行性,该方案无需对机舱和轮毂做大的调整。这对我们的客户是很有吸引力的。” Martin表示。SG 14-236 DD海上风机的扫风面积达到43500平方米,年发电量比SG 14-222 DD增加5%。该风机通过功率提升功能可以进一步将最大出力提升到15MW。Martin补充道:“西门子歌美飒专注于自身的海上风机产品开发,十年来我们围绕直驱型海上风力发电技术平台采取渐进式的技术提升,能够更有效地化解海上风电发展的风险,以保证客户的收益。”目前,SG 14-222 DD样机已经在丹麦国家大型风力发电机组测试场Østerild完成吊装,并将于今年年底前完成最终的调试并投运。这一阶段性成就将有助于西门子歌美飒在2022年完成SG 14-236 DD样机的吊装。此外,今年9月西门子歌美飒宣布全球首款可回收再利用的海上风机叶片已经在丹麦完成生产。这一叶片循环利用专利技术也适用于SG 14-236 DD风机叶片,可供客户选择。西门子歌美飒的直驱型海上风机技术平台自2011年推出以来,已经见证了超过1400台海上风机的安装。截至2021年9月,西门子歌美飒在全球的海上风机装机量超过18.7 GW,排名全球第一。 来源:西门子歌美飒
2021-09-26
GWEC《2021全球海上风电报告》发布!
全球风能理事会(GWEC)近日发布的《2021全球海上风电报告》中指出,在过去一年中,全球海上风电装机保持稳定增长势头,但各国政府需要更积极地推进海上风电发展以帮助实现碳减排目标并避免气候变化最差情境的出现。 2020年全球海上风电新增装机6.1 GW,比2019年的6.24 GW略有降低,但GWEC预计2021年将是全球海上风电装机创纪录的一年。 中国在2020年实现了3 GW以上的海上风电新增并网,连续第三年成为全球最大的海上风电市场。欧洲市场保持稳定增长,荷兰以近1.5 GW的新增装机排在全球第二位,比利时位列第三(706 MW)。 报告预计,在现有风电政策的情况下,未来十年全球将新增海上风电装机235 GW,这一增量相当于现有海上风电装机的七倍。相比于去年报告,本次预测上调了15%。 截至2020年底,全球海上风电总装机量为35 GW,每年可以实现二氧化碳减排6,250万吨,相当于在道路上减少了2,000万辆汽车,同时海上风电产业也在全球创造了70万个就业机会。 根据国际能源署(IEA)及国际可再生能源署(IRENA)的最新报告,如果希望把地球温度上升控制在1.5℃以内,全球海上风电装机需要在2050年达到2,000 GW,而现在的装机量还不到这一目标的2%,2030年的预测装机量也只是这一目标的13%。 《2021全球海上风电报告》强调,为实现零碳目标,各国政府需要改善海上风电发展的政策环境,简化规划审批流程,创造良好的市场环境,并加强对电网等基础设施的投入。 GWEC的这份《2021全球海上风电报告》包含最新的市场数据,展望了2030年全球海上风电市场态势,并对海上风电产业及区域市场的情况做了介绍。报告主题包括:海上风电助力零碳目标实现、2020年市场分析、2030年市场展望、扶持政策、审批与核准、海上风电并网、金融投资、就业及培训、新兴市场、漂浮式海上风电、海上风电技术趋势、Power-to-X及制氢等。
2021-09-22
全球海上风电,中国再次领跑!
近日,全球风能理事会发布报告指出,尽管去年受新冠肺炎疫情影响,全球海上风电新增装机容量增速有所减缓,但预计今年内,全球海上风电新增装机容量将在去年基础上增长一倍以上,有望创下历史最高纪录。 其中,中国海上风电装机增速尤为引人瞩目,去年以年增300万千瓦的速度连续第三年成为全球最大的海上风电市场。 一、中国又一次领跑 在今年9月刚刚发布的《2021全球海上风电报告》(下称“报告”)中,全球风能理事会称,2020年,中国海上风电新增装机并网容量达到了300万千瓦,占去年全球海上风电新增装机总量的49%。全球风能理事会预测,今年内,中国海上风电装机总量很可能将超过英国,成为全球海上风电装机容量最大的国家。 报告数据显示,2020年,荷兰是全球海上风电新增装机排名第二的国家,去年海上风电新增装机近150万千瓦;排名第三的是比利时,新增装机70.6万千瓦。从区域来看,2020年欧洲市场保持稳定增长,而北美地区装机增长相对较慢,总计仅有4.2万千瓦海上风电并网。全球风能理事会预计,北美海上风电市场规模将在2023年后快速扩张。 从全球范围来看,2020年全球海上风电新增装机容量为610万千瓦,略低于2019年的624万千瓦,年度新增装机容量创历史上第二高。而今年,全球海上风电新增并网容量将有望超过1200万千瓦,中国仍将是贡献最多增量的国家。全球风能理事会预测,由于业界普遍认为海上风电电价补贴明年后将取消,今年中国海上风电将进入“抢装期”,新增装机有望超过750万千瓦。 全球风能理事会的数据显示,在过去的10年里,全球海上风电市场的年增速约为22%,截至2020年底,全球海上风电总装机量为3500万千瓦,其中,欧洲装机容量占比达70%。与此同时,亚洲海上风电装机在去年底迎来了“里程碑”式突破,总量超过1000万千瓦。 二、降本压力推动风机创新 全球风能理事会首席执行官Ben Backwell表示,全球海上风电产业未来将维持高速增长,并将继续“降低价格、突破风机高度和海洋深度”,同时也将带来较高的社会经济效益。 不过,报告也指出,海上风电产业目前仍面临较大的成本压力,新一代海上风机技术成为行业降本的关键。其中,大兆瓦机组是当前行业内普遍认可的降本利器。全球风能理事会分析指出,大兆瓦机组将利用更大叶片、更高塔筒提高风机单机功率,大规模应用大兆瓦机组还将有助于减少基座、海底电缆等基础设施建设的投资,从整体上降低海上风电度电成本。 全球风能理事会在报告中指出,1991年,全球首座海上风电机组的装机容量仅为450千瓦,时至今日,海上风机单机容量已大幅提升,西门子歌美飒、维斯塔斯等国际风机制造商已陆续推出了15兆瓦的海上风机机型。今年8月,中国整机商明阳智能更是推出了16兆瓦海上风机,创下当下全球海上风机单机容量之最。 值得注意的是,报告指出,除大容量机组外,另一值得关注的海上风机创新技术是直驱中速传动风电机组,这一技术在10兆瓦及以上的大兆瓦风机中有较大的应用前景。 全球风能理事会海上风电专家Henrik Stiesdal预测,下一代海上风机单机容量有望达到20兆瓦,转子直径或将达到275米。同时,报告预测,单机容量为17兆瓦、转子直径超过250米的海上风电场有望在2035年前后正式投入使用,一旦达成,海上风电的成本将进一步下降。 然而,Henrik Stiesdal也指出,海上风机技术目前仍面临着发展瓶颈,现存海上风电供应链以及基础设施不足、原材料短缺、物流运输存在短板等因素都可能限制海上风机技术的发展。 三、现有规划难以满足降碳需求 据报告预测,在各国现有的海上风电政策框架下,未来10年,全球将新增海上风电装机2.35亿千瓦,相当于在现有规模上翻七倍以上。与去年该机构发布的报告相比,本次预测将未来十年的装机预期上调了15%。 虽然海上风电装机规模增速可观,但报告同时指出,目前这一增速尚难以满足既定的气候目标。 根据国际能源署及国际可再生能源署发布的最新测算,如果要达到将地球温升控制在1.5℃以内的目标,全球海上风电装机需要在2050年达到20亿千瓦,但根据全球风能理事会的估算,现在全球装机量还不到这一目标的2%,即使到2030年,全球海上风电预测装机量也只能达到这一目标的13%。 为此,全球风能理事会呼吁,尽管过去一年中,全球海上风电装机保持稳定增长势头,但各国仍需要更积极地推进海上风电发展以帮助实现碳减排目标。 西门子歌美飒可再生能源海上业务部门首席执行官Marc Becker建议,不论是成熟还是新兴的海上风电市场,需要更加明晰的海上风电产业政策指导和监管框架,各国政府应与业界合作,降低海上风电项目的建设周期,同时成熟市场应该更多分享实践经验和教训,帮助新兴市场建立一个合理且最优的海上风电市场机制。 该报告同时强调,为实现零碳目标,各国政府需要改善海上风电产业发展的政策环境,简化规划审批流程,创造良好的市场环境,并加强对电网等相关基础设施的投入。
2021-09-02
老旧风电场“以大代小”改造提速 叶片回收循环利用迎机遇
宁夏近日发布老旧风电场“以大代小”更新试点通知,提出按照“以大代小”等基本原则开展老旧风电场更新试点工作,提出研究建立老旧风电场回收再利用机制,探索叶片等特殊废弃材料循环利用。通知提出具体目标,到2025年力争实现老旧风电场更新+增容规模合计400万千瓦以上,占宁夏全区当前风电装机的近29%。随着宁夏试点启动,业内预期国家能源局牵头制定的《风电机组更新、技改、退役管理试行办法》即将出台,风电叶片回收再利用等行业将随着老旧风机大规模退役迎来爆发式增长。 据测算,一座5万千瓦的老风电场更新后可获得原有2-3倍容量,4-5倍的发电量,因此业内将老旧风场“以大换小”更新视为中国风电发展史上又一里程碑。老旧风机的回收再利用则成为更新顺利推进的核心,尤其是最难处理的纤维增强复合材料制成的风电叶片,填埋无法自然降解并污染土壤,焚烧产生大量有毒有害气体和飞灰。据估算,2018年国内退役叶片约3400吨,到2029年将达72万吨,增长超过210倍。风电叶片的绿色循环利用势在必行,相关公司将迎来重大发展机遇。
2021-08-11
广东十四五将大力发展航空低成本复合材料产业
8月9日,广东省印发《广东省制造业高质量发展十四五规划》。《规划》称,广东将推动航空发动机及高温合金材料、航空低成本复合材料、高温涂层材料、防腐蚀、润滑材料及产业化。广州、深圳、珠海将成为广东推动航空航天产业链各环节协同发展的重要城市。 《规划》提及,航空装备、卫星及应用等高端装备制造业僵尸广东十四五期间的重点发展产业。广东将支持水陆两用飞机、高端公务机、无人机等研发制造。 其中,广州、深圳、珠海将建立航空产业创新平台,珠海将或支持建设珠海航空产业园建设,推动水陆两用飞机批量生产,加快航空发动机维修项目,航空试飞设施建设。 在先进金属材料领域,广东将依托深汕特别合作区发展航空高温合金材料。高端精细化学品和化工新材料方面,广东也提及将在汕尾、清远加快发展玻璃钢材料、航空材料等产品。 广州南沙也正在布局千亿级的航天航空产业,未来将是内地航天「第三极」、商业航天「第一极」。目前中科空天飞行科技产业化基地正在南沙建设中,这里将成为集研制、生产、实验、总装及测试于一体的固体火箭生产基地,建成后将成为内地首个全产业链商业航天产业基地。
2021-06-22
发改委:对新核准陆上风电项目中央财政不再补贴
国家发展改革委6月11日称,2021年起,对新核准陆上风电项目中央财政不再补贴,实行平价上网;2021年新建项目上网电价,按当地燃煤发电基准价执行;新建项目可自愿通过参与市场化交易形成上网电价,以更好体现光伏发电、风电的绿色电力价值。2021年8月1日起执行。 近年来,我国新能源产业持续发展。截至2020年底,风电、光伏发电装机达到约5.3亿千瓦,是10年前的18倍。国家发展改革委有关负责人说,随着产业技术进步、效率提升,近年来新建光伏发电、风电项目成本不断下降,当前已经具备平价上网条件,行业对平价上网也形成高度共识。此次调整释放出清晰强烈的价格信号,有利于调动各方面投资积极性,推动风电、光伏发电产业加快发展,促进以新能源为主体的新型电力系统建设,助力实现碳达峰、碳中和目标。 据测算,在执行各地燃煤发电基准价的情况下,2021年新建光伏、陆上风电项目全生命周期全国平均收益率均处于较好水平,资源条件好的省份的新建项目、技术和效率领先的新建项目能够实现更好的收益。 此次调整还明确,2021年起,新核准(备案)海上风电项目、光热发电项目上网电价由当地省级价格主管部门制定,具备条件的可通过竞争性配置方式形成,上网电价高于当地燃煤发电基准价的,基准价以内的部分由电网企业结算。鼓励各地出台针对性扶持政策,支持光伏发电、陆上风电、海上风电、光热发电等新能源产业持续健康发展。 负责人表示,这有利于各地结合当地资源条件、发展规划、支持政策等,合理制定新建海上风电、光热发电项目上网电价政策。文章来源:http://www.chinacompositesexpo.com/cn/news-detail-12-10942.htm
2021-05-25
生物复合材料更多应用于飞机设计
轻质和高强的先进材料在低能耗、高性能飞机制造过程中一直发挥着关键作用。随着技术的进步,以及人类不断呼吁关注气候和可持续发展问题,在航空全产业链执行“脱碳”策略已经成为行业共识。近年来,从自然界生物中获得的原材料,以及由此制成的生物复合材料,为飞机设计师和材料工程师提供了改善未来飞行器气动性能和环境性能的新选择。 50年前,超过70%的飞机都是由一种材料制成的,即铝。大到机身和机体结构部件,小到发动机的主要零件,随处可见铝合金的身影。铝合金重量轻、成本低廉的特点,使其在航空工业中拥有了广泛应用基础。从那时起,一代又一代金属材料(钛、钢、新型铝合金、高温合金),先进复合材料(碳纤维、玻璃纤维、聚合物树脂)以及其他尖端新材料的不断涌现和应用,持续改善飞机结构设计和燃油效率。近年来,随着工程师致力于进一步释放未来飞机的潜力,新兴的一类高性能材料——生物复合材料正在为进一步改善飞行性能和环境性能提供更多可能。 近日,空客公司官网刊文,对目前应用较多、未来应用前景较好的生物复合材料进行了介绍。 生物复合材料:轻质且可回收 正如目前广泛应用于飞机制造的复合材料一样,生物复合材料也是由基体(树脂)和增强体(纤维)构成,不过所有的基体和增强体都来自自然生物,或由自然界中的生物质转化制造而成。由于具有众多的优势——轻质、灵活、经济、高效且可回收的特点,生物复合材料目前得到了越来越多的应用。 生物复合材料的原材料来自可再生资源:如生物质、植物、农作物、微生物、动物、矿物质甚至是生物废料等。这些原材料需要通过物理、化学手段转化为生物复合材料。生物复合材料可以单独使用,也可以与传统材料(如碳纤维、玻璃纤维等)互补使用。 常见的生物复合材料可由以下一种或几种组成: 天然纤维:可从动物、植物或矿物质中获得的纤维,不过不需要碳化过程(即将有机物质转化为碳或含碳残留物的过程)。 生物质碳纤维:生物质(如藻类、纤维素、木质素)主要用于生产原料以及进一步转化为纤维和树脂的原材料。 生物树脂:树脂是高粘性物质,可以转化为聚合物。生物树脂来自生物体,主要来源包括植物油、生物质或生物废物等。 在航空航天工业中,生物复合材料可用于以下领域: 客舱和货舱:客舱和货舱内零部件需要符合可燃性、烟密度和毒性以及散热性等相关要求。 一级和二级结构:这些部位涉及较高的结构载荷,因此需要改善机械性能和疲劳性能。 辅料:主要应用于飞机非主承力结构来实现辅助性功能的材料,或在工厂中生产复合材料部件所需的辅助材料。 生物复合材料中常用的原材料 甘蔗废料也称为“蔗渣”,由甘蔗茎中提取汁液后获得,是一种干燥纸浆状材料。由于甘蔗是太阳能的“高效转换器”,因此能够产生大量的生物质。 甘蔗废料是纤维素纤维的重要优质来源,可用作生物复合材料的“填充剂”,也可通过化学转化或生物精炼的方式获得生物基呋喃树脂。呋喃生物基聚合物与恰当的天然纤维或回收的纤维(例如,回收得到碳纤维等)结合使用,可应用到飞机内饰结构中。 无论是微观物种还是大型海藻,水藻类都是简单的光合作用生物,能够结合大气中的二氧化铁并将其转移为生物质。 就像其他生物质一样,水藻可作为碳原料,主要用于生产目前在传统复合材料中应用碳纤维的前驱体或树脂的单体。利用这种方式获得的生物复合材料可以提供与当前应用在飞机上的现有复合材料相同的机械性能。 玄武岩纤维是以天然玄武岩拉制的连续纤维,是玄武岩石料在1450~1500℃熔融后,通过铂铑合金拉丝漏板高速拉制而成的连续纤维。天然玄武岩属于基性火山岩,主要存在于地球洋壳和月球月海中,也是地球陆壳和月球月陆的重要组成物质。玄武岩纤维无害,具有出色的抗冲击性和耐火性,其机械性能与玻璃纤维相似,但由于其组分并不复杂,因此具有制造工艺更简单的优点。 这种直接从自然玄武岩中制造的纤维可在多领域取得不同的应用效果。其中包括可稳定登月站3D打印结构,产生隔热效果,改善过滤系统,同时也可为宇航服提供编织材料。 竹是一种轻质、可快速生长且具有高弹性的生物,同时也是一种天然复合材料,主要由嵌入木质素基质中的纤维素纤维组成。 天然竹纤维与生物基体或传统树脂基体相结合可以带来许多好处,例如,减少环境影响和改善机械性能等。
2021-03-15
GE新工厂落地英国 专门生产107米海上风电叶片
GE Renewable Energy公司(后简称GE)于3月10日宣布,计划在英格兰东北部提赛德(Teesside)城郊工业区(英格兰提斯河下游河谷和入河口附近)开设新的叶片制造工厂,该地区最近被指定为英国最新的8大自由港之一。该工厂计划由LM Wind Power主导建立并运营,未来将专门生产其107米长的海上风力发电机叶片,这是GE Haliade-X的关键部件。有关新工厂的建设和融资条款正处于相关各方进行谈判的高级阶段。 GE预计新工厂将于2023年投产,将为该地区创造多达750个直接就业岗位和1500个间接就业岗位。新厂的建立将有力支持英国政府发展就业、基础设施和供应链的计划,以实现其到2030年将海上风电装机容量提升至40GW并成为绿色能源全球领导者的目标。Teesside厂区规划图 GE指出,这是与英国政府、提斯谷工业区区长,提斯区工会及提赛德市政当局等关键利益相关者建立牢固合作关系的结果。 “GE海上风电项目的落地,将帮助提赛德自由港进一步推动绿色工业革命。” 3月初英国首相鲍里斯·约翰逊在到访时表示。 英国可再生能源协会(Renewable UK)首席执行官Hugh McNeal补充说:“GE新叶片制造厂将把提赛德从以前的钢铁厂改造成高科技清洁能源工厂,在英国供应链中创造成千上万的高技能岗位,标志着下一代海上风电制造的开始。” 据报道,位于约克郡东海岸125至290公里之间的Dogger Bank海上风电场将直接受益于这家新工厂生产的叶片。 GE表示,该风场三期项目建成后的总装机容量将达到3.6GW,足以为英国的600万户家庭供电,到2026年建成时,它将成为世界上最大的海上风力发电场。LM Wind Power的107米风叶抵达英国Blythe进行测试 Dogger Bank风电场项目总监Steve Wilson表示:“零我们感到非常自豪的是,Dogger Bank风电场是GE新叶片制造厂的锚定项目,也是GE在提赛德这项重要投资的催化剂,它利用了当地的技能和专业知识,并为英国的海上风电行业带来了长期利益。”
2021-02-01
三菱重工与维斯塔斯的新合资公司MHI Vestas Japan开始运营
自2021年2月1日起,三菱重工日本有限公司(MHI)与丹麦维斯塔斯风力系统公司(Vestas)新成立的合资公司——三菱重工维斯塔斯日本公司(MHI Vestas Japan Co.,Ltd.)开始运营,以加强两家合作伙伴在可再生能源,主要是风力涡轮机领域的市场影响力。新公司将负责在日本进行陆上和海上风力涡轮机的营销。三菱重工维斯塔斯日本公司的总部位于东京中部千代田区。 三菱重工维斯塔斯海上风电公司(MHI Vestas Offshore Wind)的前亚太地区经理Masato Yamada将担任新公司首席执行官;丹麦维斯塔斯风力系统公司总裁兼首席执行官Henrik Andersen和三菱重工能源事业部总裁兼首席执行官Kentaro Hosomi将任职新公司董事,新合资企业的持股比例为三菱重工(MHI)70%,维斯塔斯(Vestas)30%。随着三菱重工维斯塔斯日本公司的成立,三菱重工和维斯塔斯公司希望进一步利用三菱重工维斯塔斯海上风电公司的所建立的技术和经验。新合资公司除了帮助扩大陆上和海上风力发电的用途外,还将整合合作双方的卓越技术能力和丰富经验,从而加快全球脱碳计划的步伐。
2021-01-22
我国首个3.35米直径复合材料贮箱原理样机诞生
1月22日,我国首个3.35米直径复合材料贮箱原理样机在航天科技集团一院(火箭院)诞生。该贮箱主要应用在液氧环境下,相比金属贮箱可减重30%,强度更高,能够大幅提高火箭的结构效率和运载能力,是一种新型轻质贮箱。复合材料贮箱原理样机的诞生,标志着我国打破国外垄断,成为全球少数几个具备复合材料贮箱设计制造能力的国家。3.35米直径复合材料贮箱原理样机突破十大关键技术该项目是由火箭院总体设计部抓总,航天材料及工艺研究所与国内多个高校共同参与的典型“产、学、研”联合攻关项目,研究团队历时两年多,攻克了十大关键技术。复合材料液氧贮箱结构设计技术低温复合材料细观损伤力学分析技术多尺度复合材料渗漏抑制技术低温液氧相容树脂体系制备技术分瓣式可拆卸复合材料工装设计制造技术复合材料工装精确装配技术高精度自动铺放技术超薄预浸料制备技术复合材料法兰密封技术复合材料可靠粘接密封技术用于拆装复合材料组合式工装的型架研制人员初体验总体设计部贮箱组组长刘德博:“研制中要攻克从材料体系到设计制造一系列难题,许多技术都属于国内首次尝试。”总体设计部贮箱设计师张健:“制造工艺对复合材料性能影响较大,将该材料用于密封要求极高的推进剂贮箱,特别是超低温介质贮箱是一项艰巨挑战。”航天材料及工艺研究所工艺师张建宝:“箱体制造流程、工装的制备、箱体成形、工装拆除、密封检测等均充满巨大挑战,经过十几轮工艺及方案迭代才实现了样机的成功制备。”相比于金属贮箱减重30%贮箱作为火箭结构重量占比最大的部段,其减重对火箭运载能力的提升具有重大意义。材料小知识复合材料的密度为1.7g/cm³左右,铝合金密度为2.8g/cm³,铝锂合金密度为2.7g/cm³,复合材料的比强度是铝合金的8倍,是铝锂合金的6倍。在航天领域,我国现役火箭的部分部段就大量采用复合材料,减轻了结构重量。复合材料与当前火箭贮箱结构采用的金属材料相比,具有密度更小、比强度更高、抗疲劳强度更好等优势。相比于金属贮箱,复合材料贮箱可以减重30%左右,可大幅降低结构重量,提升火箭运载能力。因此,发展复合材料贮箱是实现火箭减重目的的关键技术之一,也是国际航天大国争相探索的新领域。3.35米直径复合材料贮箱原理样机的成功研制,标志着我国掌握了从复合材料贮箱结构设计、材料制备到成形制造的全链路技术流程,成为全球少数几个具备复合材料贮箱设计制造能力的国家。综合成本降低25%火箭运载能力越大,进入空间能力相对也会大幅提高,为中国航天开拓更大的舞台。贮箱结构重量占箭体结构总重的50%以上,因此,贮箱轻量化是提高火箭运载效率的重要途径之一。与应用于液氢液氧环境下的金属贮箱相比,复合材料贮箱主要应用在特定的液氧环境下,可以用在火箭末级。据资料显示,火箭末级贮箱每减重1公斤,意味着运载能力提升1公斤。而且复合材料贮箱具有生产工序少、周期短等优势。从国外的研究成果来看,相比于金属贮箱,采用复合材料贮箱可降低火箭综合成本25%。未来,复合材料贮箱在火箭末级推广应用,将能大幅提升火箭的运载能力,对探索降低火箭成本具有深远影响。复合材料贮箱自动铺放工艺原理样机的成功研制只是我国复合材料贮箱技术发展迈出的一小步,只是其中的一个里程碑。总体设计部结构室副主任吴会强介绍,后续研制团队还将对3.35米复合材料贮箱原理样机开展一系列的考核试验和评价,进一步开展关键技术攻关,提升复合材料贮箱的技术成熟度,推进复合材料贮箱在火箭上的应用,真正发挥复合材料贮箱在轻质高强方面的重大优势,实现未来火箭结构大幅减重和运载能力的提升,增强我国深空探测的能力和水平。
2020-06-15
感应焊接技术创新让热塑性复材飞机更近一步
法国焊接学院(IS)集团在焊接金属方面拥有100多年的经验,目前正成为焊接热塑性复合材料的领导者。IS集团开发了“动态感应焊接”工艺,在空客旗下STELIA航宇的航空热塑性复合材料演示项目中,被用于连接碳纤维/聚醚酮酮(PEKK) 单向带桁条和机身蒙皮。尽管这项工艺很成功,但是由于在界面处没有感受器,因此在粘结桁条的半径性能和壁板全局加热方面存在局限。感受器是置于热塑性复合材料焊接接头的两个被粘结物之间的材料,该材料被焊接头中的感应线圈加热。感受器可以是电阻加热的导电体,也可以是磁滞加热的磁性体, 在焊接界面熔化基体,同时将基体压在一起以形成具有很高强度的熔接接头。用于感应焊接热塑性复合材料的感受器最初是一种金属筛网或网格,有时浸有聚合物。 IS集团与热塑性材料供应商阿科玛建立了合作伙伴关系,共同开发并获得了专利技术,称为焊接创新解决方案。焊接创新解决方案的基础焊接创新解决方案的基础是使用感受器来加热焊接界面,但这是与焊接头相连的可移动感受器。感受器使工艺能够完美地定位焊缝的加热区域,而带有感受器的焊头是移动的,因此界面中没有残留物,不会干扰焊接结构的性能。在感应焊接的早期迭代中,金属网格感受器保留在焊缝中,但这并不是想要的结果。由于普通的航空航天层压板中的碳纤维是导电的,最新的技术已经能够消除感受器,这也使得能够使用碳纤维材料作为感受器。焊接创新解决方案的另一特点是在焊接界面处使用纯热塑性基体或低纤维量的铺层,以增加树脂流动性。可以调节该界面层的熔融温度和粘度,并且还可以进行功能化,提供导电性或隔离性,以防止电腐蚀,例如碳纤维与铝或钢之间的电腐蚀。焊接创新解决方案的成果该解决方案的接头系数为80%~90%。接头系数与焊接强度相对应,用于金属、塑料和复合材料。在对使用该解决方案将焊接在一起的两个预固化板进行的单搭剪切试验中,获得了未经焊接、热压罐固化的参考板的80%~90%的性能。这些试验使用了由赫氏Hextow AS7碳纤维和阿科玛Kepstan 7002 PEKK制造的单向带。焊接创新解决方案可用于焊接任何种类的基体:PE、PA、PEKK、PEEK以及碳、玻璃或芳纶纤维增强的热塑性复合材料。而且,还可以焊接具有铜网格的组件以防雷击,这是航空结构制造的关键。焊接创新解决方案的设计是完全自动化的,焊接头安装在6轴机械臂机器人上。焊接温度控制金属网格感受器在受到磁场作用时的一个普遍问题是所焊接零件的温度分布不均匀。该解决方案通过使用感受器来熔化焊接界面来控制这一点,使用激光高温计感知温度,该高温计实际上是从侧面测量感受器边缘的。因此,可以知道界面处的确切温度。还使用冷却方法来帮助控制温度,并确保整个焊接过程中热塑性材料能够充分结晶。桁条蒙皮焊接试验 空客旗下STELIA是这种感应焊接工艺的首批客户之一。IS集团和阿科玛为STELIA进行了一项专门研究,将7层碳/PEKK桁条焊接到14层的蒙皮上,并用铜网格覆盖以防雷击。最终目标是焊接长度为30米、具有直线和双弯曲截面的结构。使用包括Tenax HST45碳纤维和Kepstan 7002 PEKK的194 gsm单向带制作组件。STELIA规定了一种均质焊缝,其机械性能大于热压罐固化的参考材料的85%,而被粘物的热或力学性能不会退化。STELIA还要求开发一种改变被粘物厚度的鲁棒性工艺。IS集团对焊接组件进行了化学和性能试验。IS集团和阿科玛能够满足STELIA的要求,与热压罐固化的参考层压板相比,达到了大于单搭剪切和层间剪切强度性能的85%。组件层压板或防雷击网格中没有散开或退化。唯一不足的方面是速度,STELIA要求焊接速度大于等于1米/分钟。目前, 该解决方案的速度为每分钟0.3米。可以焊接的基材厚度方面, 可以焊接航空航天结构的典型厚度,并将5毫米厚的零件焊接到5毫米基底上。技术机遇与挑战IS集团和阿科玛是焊接创新解决方案技术的共同所有人,并通过可靠的专利组合保护了该技术,该专利组合已经包括五项法国和国际专利申请。焊接创新解决方案可以与任何热塑性复合材料基体一起使用,IS集团正在通过与欧美公司合作的计划来演示该技术。对于阿科玛来说,重点是PEKK, 其与赫氏在2018年结成了战略联盟关系,为未来飞机开发碳/热塑性带,着重于为客户提供更低的成本和更快的生产速度。作为合作伙伴关系的一部分,法国将建立一个联合研发实验室。这项耗资1350万欧元、为期48个月的用于自适应结构的高度自动化集成复合材料项目是阿科玛与赫氏战略联盟的延续。项目将优化用于复合零件生产的材料的设计和制造,以期实现具有竞争力的成本。它还将开发一种生产效率更高的复合材料放置/铺放技术,以及一种带有在线质量控制的、通过焊接装配最终零件的新系统。目标应用包括飞行器的主结构,汽车行业的结构零件以及石油和天然气行业的管道。热塑性材料提供的可回收性和可持续性优势对于这些市场也很重要,并将在项目中进行展示和量化。与2017年相比,与动态感应焊接工艺相比,焊接创新解决方案可以提供的好处之一是所需电力减少了50%以上。使用常规感应,需要大功率来加热表面, 但是在界面处有了感受器的话, 加热的表面要小得多,所需的能量也要少得多。这也有助于避免桁条半径振松,如果加热过多, 会软化半径上的材料,并让此处的纤维移动。但是,仍然存在散热问题。对于扁平形状,热控制非常简单,但是随着形状复杂度的增加,它变得更具挑战性。目前,主要目标是继续开发并实现典型尺度的蒙皮上桁条焊接,重点还是将技术引入新的飞行器开发计划中。
2020-06-04
14MW风机111m叶片采用碳玻混合复材主梁降低成本
为了给11-15 MW风力发电机的开发奠定技术基础,德国aerodyn公司初步设计了一款14MW风机,将采用111m的TC1B型风机叶片,该叶片的主梁采用碳纤维-玻璃纤维混合增强复合材料制造,将成本较高碳纤维的使用量降低到最低限度。现代的结构设计概念,加上aerodyn公司超过30年的风机叶片开发经验,造就了适用于14 MW风机的TC1B风机叶片。该叶片可根据额定功率、风机类型、风电场环境等具体情况进行调整和优化。该叶片的开发过程采用了最先进的材料和制造技术。在14 MW的额定功率下,aerodyn公司的风机叶片能够实现228 m的叶轮直径、额定转速7.54 rpm、叶尖额定转速90 m/s。同时,14 MW风机叶片保持了7.018 m的最大弦长,叶尖预弯4 m。此外,叶根螺栓圆直径(根部节圆直径)达到5050 mm。 目前,该公司的工作重点是对10 MW风机的开发,10 MW风机将于明年投入生产。下一步,更大功率的风力发电机(约15 MW)将在2025年前后面市。目前,供应链和必要的基础设施是实施未来计划的巨大挑战。